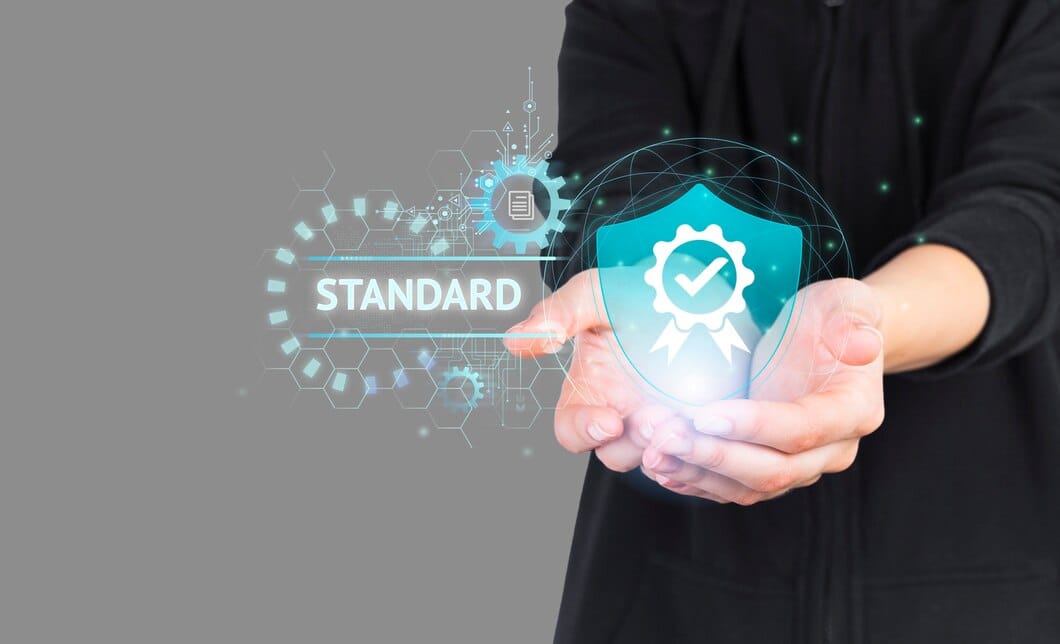
Quality management in factories is one of the key factors in ensuring the success and sustainability of any industrial facility. Quality management plays a vital role in improving production processes, raising efficiency, and reducing costs, which ultimately leads to meeting customer requirements and achieving their satisfaction.
Implementing a quality management system is not only limited to improving production, but also contributes to improving the factory’s image and increasing its competitiveness in the market.
The concept of quality management in factories
Quality management in factories means implementing a set of systems and procedures that ensure that the products or services provided meet the pre-determined quality standards. Its main goal is to produce defect-free products, while reducing waste and improving the overall efficiency of the factory. This management is implemented through comprehensive monitoring of all stages of production, starting from receiving raw materials to the exit of the final product.
Main benefits of implementing quality management systems in factories
1- Improving product quality: Quality management systems help ensure the production of high-quality products that meet or exceed customer expectations.
2- Increasing production efficiency: Reduces waste and improves workflow within the factory, which contributes to reducing costs.
3- Compliance with international standards: Quality systems help ensure that factories comply with international requirements and standards, such as ISO standards.
4-Achieving customer satisfaction: Good products that comply with standards enhance customer satisfaction and loyalty to the factory.
5-Reducing defects and failures: Quality systems contribute to quickly detecting and analyzing defects, which helps reduce future failures.
Common quality management standards and systems in factories
There are several quality management systems and standards that can be applied in factories to ensure high quality and achieve production goals efficiently. The most prominent of these systems are:
ISO 9001
ISO 9001 is one of the most famous international standards concerned with quality management in factories. This certificate is based on a set of principles such as customer focus, effective participation of senior management, and a process-based approach. This certificate works to improve and standardize processes in line with international requirements.
HACCP (Hazard Analysis and Critical Control Points) System
This system is used specifically in the food industry, and aims to identify potential hazards at different stages of production and take appropriate preventive measures to control them. Applying quality management in factories through HACCP ensures that food products are safe and free from contamination and health risks.
GMP (Good Manufacturing Practice) Certification
GMP is one of the most important quality systems, especially in the pharmaceutical and food industries. This certification helps ensure that products are produced in a way that meets high quality standards and reduces the possibility of defects or health problems.
Steps to implement quality management in factories
1- Determine goals and standards
The first step to implement quality management in factories is to define the goals and standards that the facility wants to achieve. These goals must be measurable and clearly defined to ensure continuous improvement of operations.
2- Training employees
Quality systems cannot be implemented without qualified employees trained to understand the required principles and procedures. The factory must provide training programs for employees at all levels.
3- Monitoring operations and analyzing results
Implementing quality management in factories requires careful monitoring of all stages of production and analyzing the extracted data. Through this analysis, areas that need improvement can be identified and appropriate corrective actions can be taken.
4- Periodic review and continuous improvement
Periodic review of the results of quality systems contributes to identifying strengths and weaknesses and taking the necessary steps to continuously improve operations. Continuous improvement should be an essential part of the factory culture to ensure that quality remains high.
Certifications required for quality management in factories
To achieve high levels of quality management in factories, industrial facilities must obtain some certificates that enhance their credibility and confirm their commitment to international standards. The most important of these certificates are:
1-ISO 9001 Certificate
As mentioned earlier, ISO 9001 Certificate is one of the basic certificates that factories need to ensure their compliance with international quality standards.
2-ISO 14001 Certificate
This certificate relates to the environmental management system and ensures that the factory is committed to applying environmentally friendly practices in all its production stages.
3-ISO 22000 Certificate
It is considered one of the important certificates in the food industry, as it ensures that the factory applies a food safety management system according to international standards.
The Role of Technology in Improving Quality Management in Factories
In the era of digital transformation, technology has become one of the main elements in quality management in factories. Modern technologies such as smart systems, artificial intelligence, and the Internet of Things contribute to improving product quality, reducing waste, and improving overall factory efficiency. By applying automated quality control techniques, factories can reduce human errors and ensure a higher level of quality on an ongoing basis.
The Importance of Effective Communication in Quality Management
Communication plays an important role in the success of quality management in factories. Implementing quality systems requires continuous communication between all departments and administrations to ensure coordination of efforts and working as a team to achieve common goals. This communication includes effectively exchanging information about challenges and progress made at various stages of production. It is essential to have open and clear channels for conveying quality-related information to both employees and managers, which enhances everyone’s understanding of the importance of adhering to quality standards.
Quality Control and Continuous Improvement
The quality control process plays a major role in maintaining a high level of performance and ensuring that final products meet the required standards. This is achieved through periodic inspections and tests conducted on products throughout all stages of production. Quality management in factories also relies on continuous feedback from this monitoring to identify areas that need improvement. By applying the concept of continuous improvement, factories are committed to developing their operations periodically to ensure the provision of better and more efficient products.
Challenges facing quality management in factories
Despite the great benefits of implementing quality management systems in factories, factories face several challenges that may hinder the implementation of these systems. Among these challenges are:
1-Internal resistance to change: Often, the implementation of quality systems may face resistance from employees who are accustomed to certain ways of working.
2-Initial costs: Implementing quality systems may require significant financial investments at the beginning, including employee training, purchasing new equipment, or improving infrastructure.
3-Difficulty adapting to international standards: Some factories may find it difficult to meet the precise requirements of some international certificates, which requires continuous reviews and adjustments to operations.
Applying sustainability standards in quality management systems
Focusing on sustainability has become an integral part of quality management in modern factories. Factories are now moving towards implementing systems that preserve the environment and reduce the consumption of natural resources. Some international standards such as ISO 14001 are based on environmental quality management, ensuring that the factory operates according to strict environmental standards. These standards not only help in preserving the environment, but also increase the factory’s ability to meet the expectations of customers who care about sustainability.
In conclusion, implementing quality management systems in factories is a vital step towards improving production processes and ensuring customer satisfaction. The success of these systems depends on providing the necessary training for employees, adopting the required certificates, and using technology to improve performance.
In this regard, ProNano Food Industry Consulting can provide specialized consultations for those interested in implementing quality management systems in factories, as the company provides integrated solutions to improve quality and provide support in obtaining internationally recognized certificates. For more information about the company’s services and how to benefit from them, you can contact the team of experts directly.
Read more about food safety and quality consulting and halal food consulting