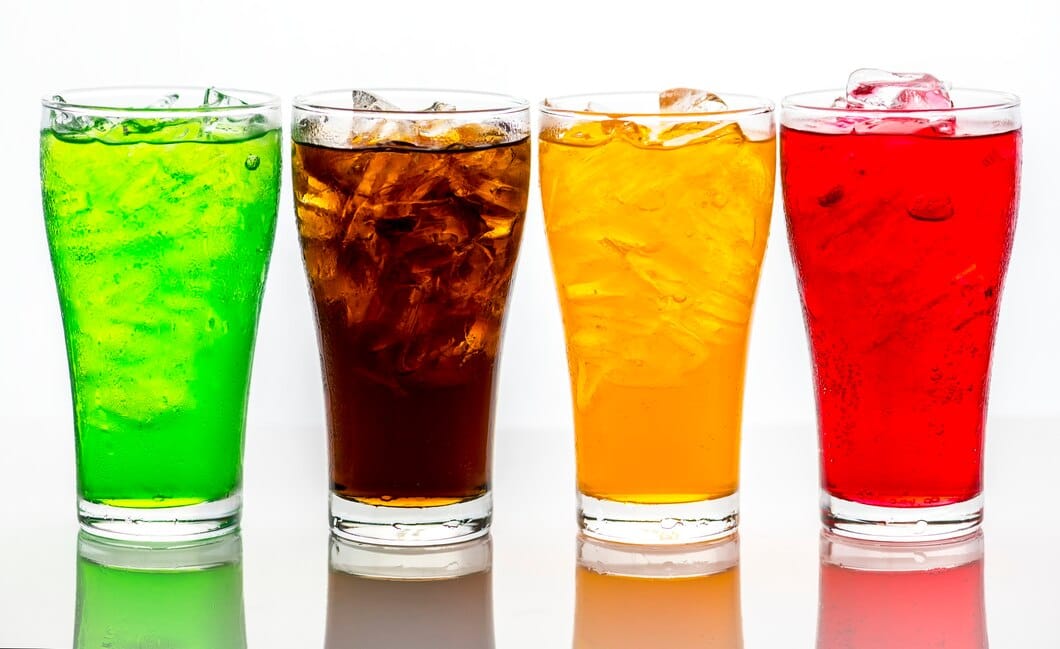
The soft drink industry is an important economic sector, as its products are very popular in local and international markets. If you are thinking of launching a soft drink factory project, there are several aspects that must be taken into account to achieve success.
In this article, we will review the steps to establish a soft drink factory project, the basic requirements, and current trends in the soft drink industry.
Steps to establish a soft drink factory project
1- Feasibility study
The first step in establishing a soft drink factory project is to conduct a comprehensive feasibility study. This study should include market analysis, identifying competitors, and estimating potential costs and revenues. It should also address supply and demand factors, and consumer trends.
2- Selecting a location
Choosing the right location is a critical factor for the success of the project. It is preferable for the factory to be close to sources of raw materials, in addition to its proximity to target markets to reduce transportation costs. It is also important to ensure that the necessary infrastructure such as electricity and water is available.
3- Obtaining licenses
Before starting production, the necessary licenses must be obtained from the relevant authorities. These licenses include manufacturing licenses, health licenses, and any other permits that may be required in your country. Compliance with health regulations and standards is essential to ensure product safety.
4- Factory Setup
Factory setup requires a significant investment in equipment and technology. Highly efficient filling and packaging machines, water filtration and purification systems, and quality control devices should be selected. This will help improve productivity and reduce waste.
5- Product Development
Developing innovative and distinctive products is an essential part of the success of a soft drink factory project. This stage should include testing flavors, developing new recipes, and offering healthy options such as sugar-free or low-calorie soft drinks.
Soft Drink Manufacturing Components
1-Water
Water is the main ingredient in any soft drink. Water must be clean and free of impurities, as its quality affects the taste of the final product.
2-Sugars
Sugars are a major source of energy, and give soft drinks their sweet taste. Regular sugar, sugar substitutes, or artificial sweeteners can be used. The impact of each type on the health of the consumer must be studied.
3-Carbon dioxide
Carbon dioxide is used to give bubbles to carbonated drinks. It is introduced into the product during the filling process, and affects the product’s flavor and texture.
4-Flavors and colors
Flavors and colors are essential elements to attract consumers. Natural or synthetic ingredients must be carefully selected to ensure that customer expectations are met.
Trends in Soft Drinks Industry
Health Focus
The growing health awareness among consumers has led to a demand for healthy soft drinks. Many now prefer sugar-free or low-calorie options. Therefore, developing healthy products is one of the key trends that a soft drink manufacturer should focus on
Sustainable Packaging
Sustainability has become a hot topic in the food and beverage industry. Many companies are moving towards using recyclable or environmentally friendly packaging materials, making the project more attractive to consumers
Flavor Innovation
Consumers are now more inclined to try new and unconventional flavors. Therefore, soft drink manufacturers should consider developing unique flavors, such as blending fruits and herbs
Supply and Raw Materials When Establishing a Soft Drink Factory Project
Selecting Suppliers
It is essential for a soft drink factory project to select reliable suppliers to secure raw materials. This includes water, sugars, flavors, and colors. Suppliers should be evaluated based on the quality of materials, prices, and reliability of delivery. Negotiating the right contracts can reduce costs and ensure continuity of production
Quality Control
Controlling the quality of raw materials is an essential part of the success of a soft drink manufacturing project. Regular tests should be conducted to ensure that all components meet the required health and quality standards. This will enhance customer confidence in the final product and reduce the chances of any problems occurring during the production stages
Choosing the Right Technology for a Soft Drink Factory Project
Production Equipment
When establishing a soft drink factory project, you must consider choosing the right technology for the factory. This includes choosing highly efficient machines for filling and packaging drinks, as well as systems for filtration and ensuring water quality. Investing in modern technology can improve productivity and reduce waste
Automation of production processes
Automation plays an important role in improving the efficiency of operations. Automated systems can help reduce human error and increase production speed. For example, using automated quality control systems can ensure that every bottle leaving the factory meets the required standards
Food Safety and Compliance
Safety Standards
Food safety is a top priority in any soft drink factory project. Health standards approved by local and international bodies must be adhered to. This can include equipment sterilization procedures, temperature monitoring during storage, and ensuring the safety of workers in the factory.
Certifications and Licenses
The project must obtain the necessary certificates that prove compliance with safety standards. These certificates include ISO certificates and food safety certificates. Obtaining these certifications enhances the project’s credibility and helps attract customers and distributors.
Project Sustainability
Waste Management
Waste management is an important part of a soft drink manufacturing project. Strategies should be implemented to recycle materials and dispose of waste safely. This could include reusing raw material packaging, or using techniques to reduce waste during production.
Renewable Energy
Using renewable energy sources can be a positive step towards project sustainability. Consider installing solar panels or using wind power to reduce reliance on conventional energy. This will not only help reduce costs in the long run, but will also contribute to improving the brand image.
Innovation Strategies in Soft Drink Plant Project
Developing New Flavors
Innovation in soft drink flavors is one of the key factors for the success of a soft drink plant project. Companies should look for new flavors that are in line with changing consumer preferences. Surveys can be conducted and global trends can be analyzed to determine which flavors are likely to be popular. Experiments with unique flavors, such as blending fruits with herbs or spices, can add additional value to products.
Innovation in Packaging
Packaging methods are an essential part of the consumer experience. Soft drink plant projects can consider using innovative packaging, such as reusable bottles or biodegradable containers. Packaging innovation not only helps attract customers, but can also have a positive impact on the environment. Using modern packaging techniques can help maintain the quality of drinks and extend their shelf life.
Developing Healthy Options
With the increasing health awareness among consumers, a soft drink plant project should consider developing healthy options. This could include producing sugar-free soft drinks, reducing calories, or using natural ingredients. By offering healthier options, companies can meet the needs of consumers who are seeking a healthier lifestyle.
The success of a soft drink factory project depends on many factors, including innovation, product quality, and understanding of the market. By considering the above aspects, investors and interested parties can achieve positive results in this field.
ProNano Food Industry Consulting is ready to provide the necessary support and guidance to those interested, helping them achieve their goals in the soft drink industry. Do not hesitate to contact us for your consultation now.
Read more about the spice factory project